How to Calibrate a CNC Machine
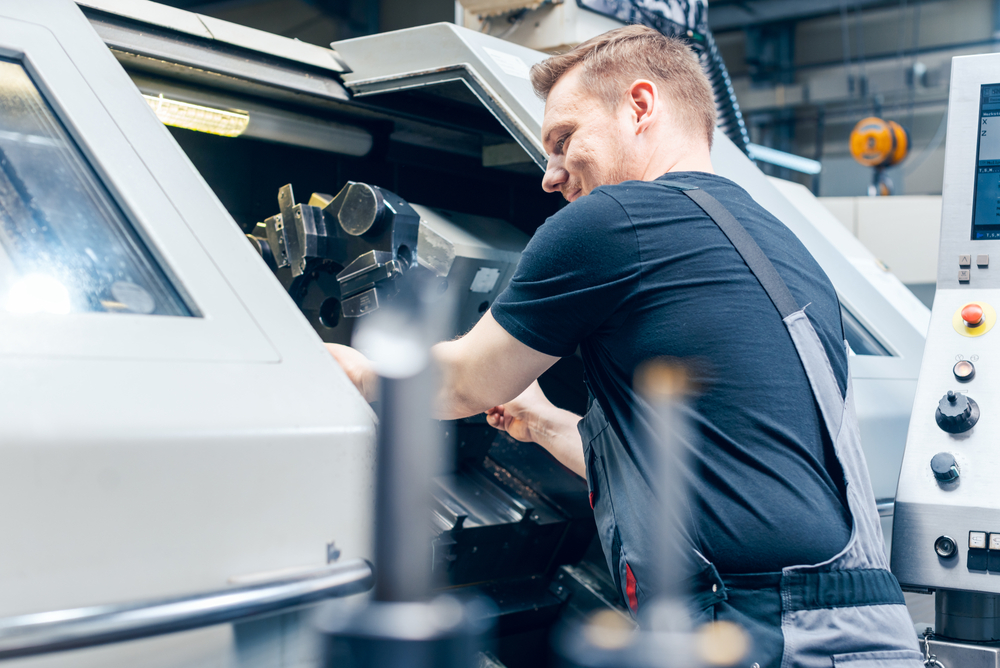
Calibrating a CNC machine is essential in ensuring precision and accuracy in the manufacturing process. A properly calibrated machine will produce consistent, high-quality results, increasing productivity and customer satisfaction.
Importance of Calibrating a CNC Machine
Calibrating a CNC machine is crucial for achieving accurate and repeatable results. Without proper calibration, the machine may produce out-of-spec parts, leading to waste, rework, and customer dissatisfaction. Additionally, a poorly calibrated machine can cause excessive tool wear and reduced life, increasing costs and downtime.
Calibrating a CNC machine also helps ensure that it is operating at its optimal performance level. By fine-tuning the machine’s settings and parameters, operators can maximize efficiency and speed while minimizing errors and inconsistencies. This ultimately leads to improved productivity and profitability for the business.
Steps to Calibrate a CNC Machine
1. Check Machine Geometry
The first step in calibrating a CNC machine is to check its geometry. This involves measuring the distance between various points on the machine, such as the spindle centerline and the worktable, to ensure that they are within tolerance. Any deviations from the specified dimensions should be corrected through adjustments to the machine’s mechanical components.
2. Check Positioning Accuracy
Next, the positioning accuracy of the machine must be verified. This can be done by performing a series of test cuts or measurements using a calibrated tool. Any errors in positioning should be corrected by adjusting the machine’s axis settings or compensating for the errors in the program.
3. Check Tool Length and Diameter
Calibrating the tool length and diameter is crucial for achieving accurate cuts and hole diameters. This can be done using a tool presetter or by manually measuring the tool length and diameter and inputting the values into the machine’s tool offset parameters. Regular checks and adjustments should be made to ensure that the tool dimensions are accurate.
4. Check Spindle Speed and Feed Rates
Another important aspect of calibrating a CNC machine is to check and adjust the spindle speed and feed rates. This can be done by running test cuts at different speeds and feed rates and measuring the results for accuracy and surface finish. Adjustments should be made to optimize cutting performance and prevent tool damage.
5. Check Axis Alignment
Proper axis alignment is essential for achieving accurate and parallel cuts. This can be checked by performing a series of test cuts in different directions and measuring the results for alignment errors. Adjustments to the axis settings should be made to correct misalignments and ensure that the machine cuts straight and true.
Tips for Maintaining Calibration Accuracy
1. Regular Maintenance
Regular maintenance of the CNC machine is essential for maintaining calibration accuracy. This includes cleaning, lubricating, and inspecting the machine’s components for wear or damage. Any issues should be addressed promptly to prevent them from affecting the machine’s performance.
2. Keep a Maintenance Log
A detailed maintenance log can help track the machine’s calibration history and identify any patterns or trends indicating the need for adjustments or repairs. It can also help schedule preventive maintenance tasks and ensure that the machine is always operating at its best.
3. Train Operators
Proper training of machine operators is crucial for maintaining calibration accuracy. Operators should be familiar with the machine’s settings and parameters, as well as the calibration procedures, to ensure that they can effectively monitor and adjust the machine as needed. Regular training sessions and refresher courses can help keep operators up to date on best practices and procedures.
4. Use Quality Tools and Materials
Quality cutting tools and materials are essential for achieving accurate and repeatable results. Inferior tools or materials can lead to poor cutting performance, increased tool wear, and reduced accuracy. Investing in high-quality tools and materials can help improve the machine’s performance and longevity.
5. Perform Regular Checks
Regular checks and inspections of the machine’s calibration are necessary to ensure that it remains accurate and consistent. This can involve running test cuts, measuring the results, and comparing them to the machine’s specifications. Any deviations should be addressed promptly to prevent them from affecting the machine’s performance.
Contact Us Today
Calibrating a CNC machine is critical in ensuring accuracy, precision, and consistency in the manufacturing process. By following the proper calibration procedures and maintaining the machine regularly, businesses can achieve high-quality results, reduce waste and downtime, and improve overall productivity and profitability.
For over ten years, MTE Bridgesaw has been a trusted provider of CNC machines for the granite industry. With a commitment to quality and reliability, MTE Bridgesaw offers a range of cutting-edge machines designed to meet the unique needs of granite fabricators. Whether you want to upgrade your current CNC machine or invest in a new one, MTE Bridgesaw has the solutions you need to take your business to the next level.
Learn more about us and our line of CNC machines, and discover how we can help you achieve precision, accuracy, and success in your granite fabrication business. Contact MTE Bridgesaw today to schedule a consultation and see how our machines can revolutionize your production process.