Why Is a CNC Granite-Cutting Machine Expensive?
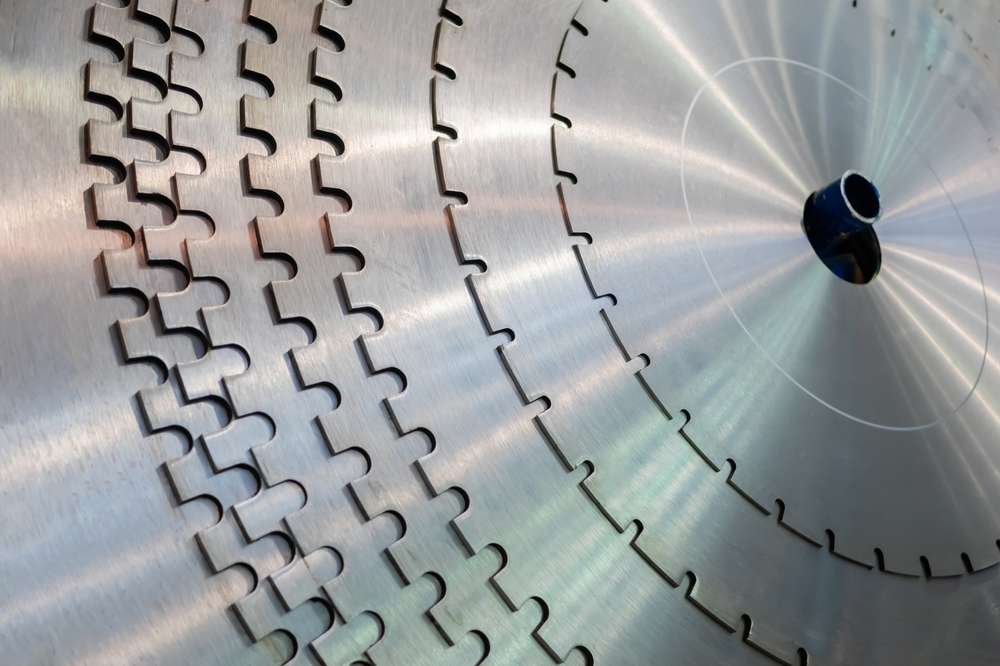
In the realm of stone fabrication, the CNC (Computer Numerical Control) granite-cutting machine stands as a pinnacle of technological advancement and precision. This sophisticated machinery has revolutionized how fabricators cut and shape granite, resulting in unparalleled accuracy, efficiency, and detail in the end products. However, the investment required to acquire such a machine is substantial, prompting a frequently asked question: Why is a CNC granite-cutting machine so expensive?
Advanced Technology and Precision Engineering
Its advanced technology and precision engineering are at the core of a CNC granite-cutting machine. Unlike conventional cutting machines, CNC models are equipped with computer systems that control and monitor the cutting process with extreme accuracy. These systems require high levels of precision to achieve the micro-level tolerances essential for cutting hard materials like granite.
The engineering behind CNC machines involves high-quality components and meticulous assembly processes. To ensure smooth and precise movements, motors, actuators, and controllers must be top-notch. The machine’s frame and body require robust construction to withstand the intense vibrations and pressures generated during cutting. All these components contribute to the overall cost, underscoring why CNC granite-cutting machines command a premium price.
Materials and Construction Quality
Granite, one of the hardest natural stones, demands cutting equipment to endure substantial mechanical stresses. The materials used in constructing a CNC granite cutting machine are generally high-strength metals and composites designed for durability and longevity. The use of stainless steel, cast iron, and other specialized alloys ensures the machine can handle heavy-duty operations without degrading over time.
Additionally, the build quality involves extensive quality control checks and precision manufacturing techniques that add to the overall costs. Makers of CNC granite cutting machines invest heavily in ensuring their products can deliver consistent performance over prolonged periods. This emphasis on quality and durability is intrinsic to the machine’s high price tag.
Software Sophistication
The brain of a CNC granite cutting machine lies in its software. Modern CNC machines are equipped with advanced software that allows for intricate designs and efficient cutting processes. This software must be not only highly functional but also user-friendly, allowing operators to input complex designs and operate the machine with relative ease.
Research and development are ongoing and costly endeavors in creating sophisticated software platforms. Continual updates and improvements are necessary to keep up with evolving user needs and technological advancements. The cost of developing, maintaining, and upgrading this software is intrinsically linked to the overall expense of CNC granite-cutting machines.
Operational Efficiency
Despite the upfront costs, CNC granite cutting machines offer operational efficiencies that can significantly lower long-term expenses for stone fabrication businesses. These efficiencies stem from automation, which reduces the need for manual labor and minimizes waste material through precision cuts. Automated processes also tend to deliver faster turnaround times on projects.
Operators can program the CNC machine to perform tasks repeatedly with consistent quality, eliminating the variability and errors associated with human labor. Additionally, the machine’s ability to work autonomously for extended periods reduces the need for continuous operator oversight, further lowering labor costs. Although these operational efficiencies are invaluable in the long term, they add to the initial investment when procuring such machinery.
Enhanced Productivity and Capabilities
A key justification for the expense of CNC granite cutting machines is the enhanced productivity and expanded capabilities they offer stone fabrication businesses. These machines are not limited to cutting; they can also perform milling, drilling, and engraving functions, adding versatility to the types of services a business can provide.
The ability to execute detailed and intricate designs with high precision opens new avenues for creativity and innovation in product offerings. Whether it is a complex kitchen countertop design, an artistic sculpture, or detailed architectural elements, CNC machines can deliver results that are not feasible with traditional methods. This capability can attract more clientele, drive revenue growth, and offer a competitive edge in the market, ultimately making the initial investment worthwhile.
Reduced Material Waste
One of the often-overlooked advantages of CNC granite-cutting machines is their ability to minimize material waste. Precision is a hallmark of CNC technology, ensuring that every cut is executed with exactitude, reducing the chances of errors leading to material waste.
Granite is an expensive material, making waste reduction an important consideration. Efficient use of materials not only cuts down costs but also aligns with sustainable practices. By investing in a CNC granite-cutting machine, businesses can maximize the utility of their granite slabs, thereby deriving more value from each piece of material and mitigating the impact of high granite costs.
Long-Term Durability and Lower Maintenance Costs
While the initial cost of a CNC granite-cutting machine is high, it is important to consider the long-term benefits and cost savings. These machines are built to last, often featuring robust components that can endure years of intensive use. With proper maintenance, their longevity can result in lower lifecycle costs compared to cheaper, less durable alternatives.
Additionally, CNC machines tend to have lower maintenance requirements. Precision engineering and high-quality components mean fewer breakdowns and repairs. Regular, preventive maintenance can keep these machines running smoothly, ensuring uninterrupted production cycles and minimizing downtime. The cumulative savings in repair costs and downtime over the machine’s lifetime can be substantial, justifying the initial investment.
Comprehensive Installation and Training Services
The cost of a CNC granite cutting machine often includes comprehensive installation and training services. These machines are complex, and proper setup ensures optimal performance. Manufacturers usually provide detailed installation services conducted by skilled technicians to ensure the machine is correctly calibrated and operational.
Moreover, proper training is essential for operators to fully utilize the CNC machine’s capabilities. Training programs provided by manufacturers or resellers cover machine operation, software use, maintenance practices, and safety protocols. Although integral to the machine’s operation, these services contribute to the overall cost. However, they ensure that businesses can efficiently and safely integrate the machine into their operations, maximizing its return on investment.
Future-Proofing and Scalability
Investing in a CNC granite cutting machine is also an investment in future-proofing and scalability. As the technology behind these machines continues to evolve, manufacturers often offer upgrade options that allow businesses to keep their equipment current without needing to purchase entirely new machines. This adaptability can make the high initial cost more palatable, knowing that the machine can evolve with the business’s needs.
Another benefit is scalability. As demand for precision-crafted stone products grows, having a CNC machine allows a business to scale its operations smoothly. The ability to handle larger projects or increase production volume without requiring significant additional labor or equipment investments makes CNC machines valuable.
Contact Us Today
At MTE Bridgesaw, we deeply understand the intricacies and value of CNC granite cutting machines. We started our journey in 2010 with the commitment to offer unparalleled service and support for stone fabrication machinery across the nation. Our journey led us to develop our own line of machines that stand out for their superior performance, power, precision, and durability, all backed by the best warranty in the industry. Today, with over 1,000 machines operating successfully across the U.S., our reputation is built on trust and excellence.
If you are considering investing in a CNC granite cutting machine, it’s essential to choose a provider who not only delivers exceptional equipment but also stands by it with comprehensive support and maintenance services. MTE Bridgesaw is dedicated to keeping your machines running optimally, ensuring uninterrupted production and maximized profitability for your business. Whether you own our machines or those from other manufacturers, our expert technicians are ready to provide the necessary care and service.
Don’t let the high initial cost deter you from reaping the immense benefits of advanced CNC technology. Contact MTE Bridgesaw today to learn more about our cutting-edge machines, superior service, and how we can help you elevate your stone fabrication business to new heights.