Choosing a CNC Water Jet Cutter
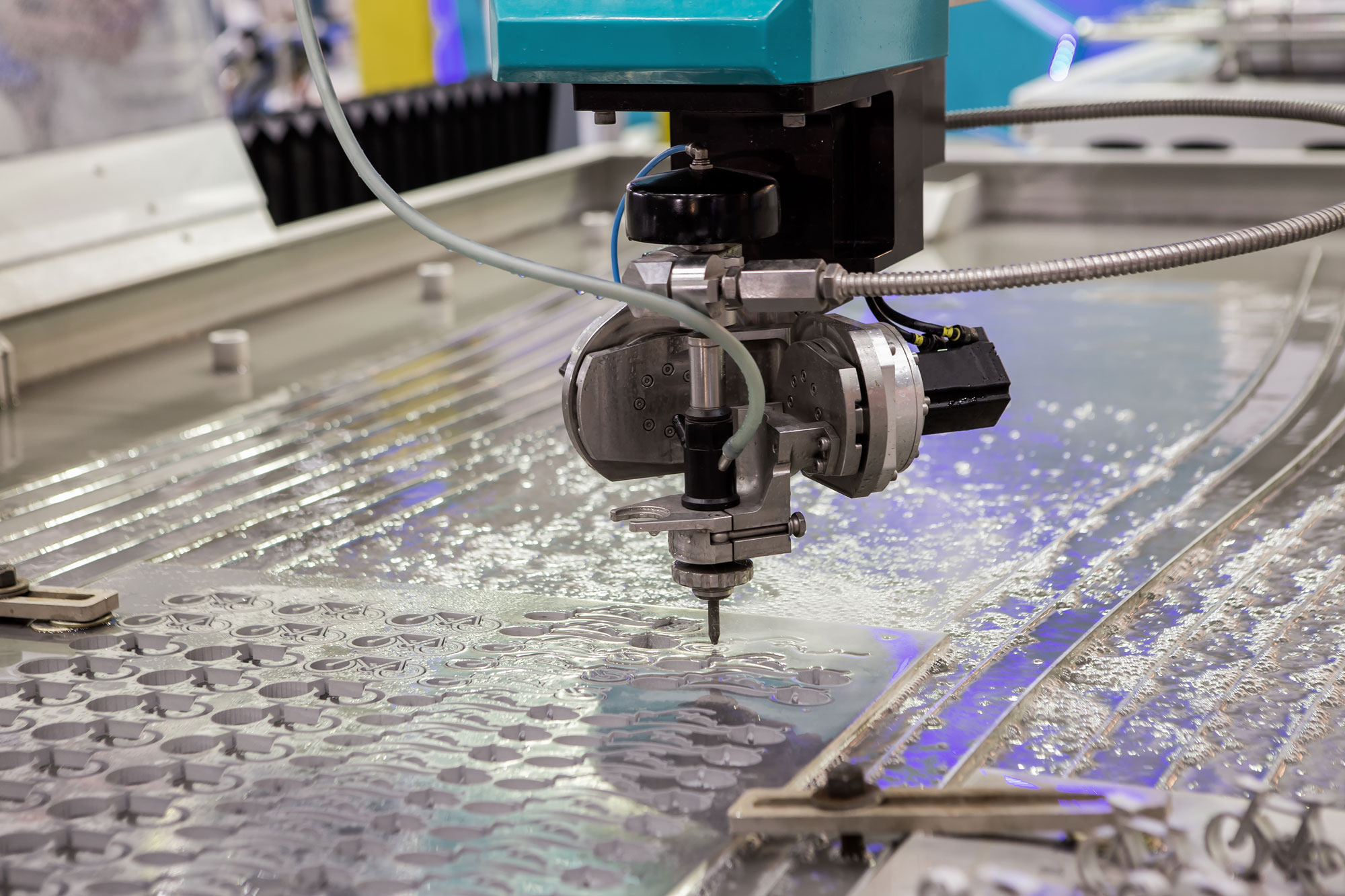
When it comes to precision cutting, few tools are as versatile and efficient as a CNC water jet cutter. These machines use a high-pressure stream of water, often mixed with abrasive materials, to cut through a wide range of materials with incredible accuracy. And whether you’re working with metal, stone, glass, or composite materials, CNC water jet cutting offers a level of precision and flexibility that other cutting methods simply can’t match.
Thankfully, at Machine Tech Enterprises, LLC, we specialize in providing high-quality CNC water jet cutters for a variety of industries. Our machines are designed to offer both durability and precision, helping our clients meet their production needs with confidence. So let us guide you through the process of choosing the best CNC water jet cutter for your specific applications, exploring key factors to consider, from material compatibility to machine size and cost.
1. Understanding How CNC Water Jet Cutters Work
Before diving into how to choose the right CNC water jet cutter, it’s important to understand how these machines work. A CNC water jet cutter uses a computer-controlled system to guide a high-pressure stream of water (often as high as 60,000 PSI or more) through a nozzle. When mixed with an abrasive substance, such as garnet, the water jet becomes strong enough to cut through a variety of hard materials.
This method of cutting is highly precise, as the CNC (computer numerical control) system allows for detailed programming and exact movements. The result is clean, intricate cuts with minimal waste, making CNC water jet cutting ideal for industries ranging from aerospace and automotive to architecture and custom fabrication.
Advantages of CNC Water Jet Cutting
- Versatility: CNC water jet cutters can handle a wide range of materials, including metals (steel, aluminum, copper), stone (marble, granite), glass, ceramics, and even softer materials like rubber or foam.
- Precision: The computer-controlled system ensures highly accurate cuts with tolerances as tight as ±0.001 inches, depending on the machine’s capabilities.
- Cold Cutting Process: Since water jet cutting is a cold process, there’s no heat-affected zone (HAZ), which means the material’s properties remain unchanged, and there’s no risk of warping or melting.
- Eco-Friendly: Water jet cutting produces minimal waste, and since no toxic fumes are released, it’s a more environmentally friendly cutting method.
Understanding these benefits is the first step in determining whether a CNC water jet cutter is the right tool for your specific project needs.
2. Types of CNC Water Jet Cutters
There are two main types of CNC water jet cutters: pure water jet cutters and abrasive water jet cutters. The type you choose will depend largely on the materials you need to cut.
Pure Water Jet Cutters
Pure water jet cutters use a high-pressure stream of water without any abrasive material. These machines are best suited for cutting soft materials, such as foam, rubber, plastics, or food products. While pure water jets are highly precise and can cut intricate shapes, they are not effective for cutting harder materials like metal or stone.
Ideal Applications for Pure Water Jet Cutters:
- Packaging: Cutting foam inserts, rubber seals, or plastic packaging materials.
- Food Industry: Cutting soft food products like vegetables, bread, or fish without contamination.
- Textile Industry: Cutting fabrics or materials used in apparel and upholstery.
Abrasive Water Jet Cutters
Abrasive water jet cutters, on the other hand, are designed for harder materials. By mixing an abrasive substance like garnet into the water stream, the jet becomes powerful enough to cut through metals, ceramics, glass, and stone. Abrasive water jet cutting is ideal for heavy-duty industrial applications where precision cutting of hard materials is required.
Ideal Applications for Abrasive Water Jet Cutters:
- Metal Fabrication: Cutting stainless steel, aluminum, copper, and other metals with clean edges and minimal post-processing.
- Stone and Tile Cutting: Shaping stone materials like granite, marble, and quartz for architectural projects.
- Automotive and Aerospace: Cutting composite materials, metals, and glass with precision for parts and components.
At Machine Tech Enterprises, LLC, we offer both pure and abrasive CNC water jet cutters to meet the diverse needs of our clients across various industries. Knowing which type of cutter to invest in depends on the materials you work with most frequently.
3. Key Considerations When Choosing a CNC Water Jet Cutter
Selecting the right CNC water jet cutter for your business is a significant investment, and there are several important factors to consider before making your purchase. By evaluating your needs in terms of material types, production volume, and desired precision, you can ensure that you’re choosing a machine that delivers the performance and reliability you need.
1. Material Compatibility
One of the most important factors in choosing a CNC water jet cutter is the type of materials you will be cutting. If your business primarily works with soft materials like rubber or plastic, a pure water jet cutter will likely meet your needs. However, if you’re working with harder materials like metal or stone, an abrasive water jet cutter is essential.
Consider the thickness of the materials as well. Water jet cutters are capable of cutting materials up to several inches thick, but different machines have different capacities. Make sure to choose a machine that can handle the thickness of the materials you work with most often.
2. Cutting Speed and Precision
Another key consideration is the speed and precision of the machine. CNC water jet cutters are known for their ability to deliver highly precise cuts, but cutting speed can vary depending on the machine’s power and the material being cut. For high-volume production environments, cutting speed is an important factor to ensure that you can meet production deadlines without sacrificing quality.
Some CNC water jet cutters offer adjustable cutting speeds, allowing you to strike the right balance between speed and precision for your specific needs. If you’re working on intricate designs or projects that require extremely tight tolerances, prioritize a machine with a high degree of precision over one that simply offers fast cuts.
3. Machine Size and Workspace Requirements
CNC water jet cutters come in a variety of sizes, from compact models designed for small workshops to large, industrial machines capable of handling oversized materials. The size of the machine you choose should be based on your available workspace and the size of the materials you’ll be working with.
Measure the available floor space in your shop, and consider not only the machine itself but also the space needed for loading and unloading materials. Additionally, think about whether you’ll need a machine with a larger cutting bed to accommodate oversized sheets of material, or whether a smaller machine with a more compact footprint will suffice for your operations.
4. Operating Costs and Maintenance
While CNC water jet cutters are highly efficient, it’s important to factor in operating costs when making your decision. Operating costs include the water supply, electricity, and abrasive material (for abrasive cutters). Additionally, consider the maintenance requirements of the machine. Regular maintenance is necessary to keep the cutter running smoothly and to avoid downtime, so choosing a machine with easy-to-maintain components can save time and money in the long run.
At Machine Tech Enterprises, LLC, we offer machines that are not only powerful but also designed for durability and ease of maintenance. Our CNC water jet cutters are built to last, minimizing maintenance needs and reducing overall operating costs for our customers.
5. Software and User-Friendliness
A CNC water jet cutter relies on computer software to control its precision movements, so it’s important to choose a machine that comes with intuitive and user-friendly software. Some systems are more complex than others, and choosing the right software can make a big difference in how easily you and your team can program and operate the machine.
Look for machines that offer clear, easy-to-use interfaces and software that supports a wide range of file formats (such as DXF, DWG, and others) so you can seamlessly integrate your designs into the cutting process. User-friendly software can help reduce training time and improve overall productivity.
4. Why CNC Water Jet Cutting is Ideal for a Range of Industries
One of the main advantages of CNC water jet cutting is its versatility. The ability to cut a wide range of materials with high precision makes it ideal for various industries, including:
1. Metal Fabrication
CNC water jet cutters are widely used in metal fabrication for cutting stainless steel, aluminum, and other metals with precision and without the need for secondary finishing processes. The clean, burr-free edges produced by water jet cutting eliminate the need for extensive post-processing, saving time and labor costs.
2. Aerospace and Automotive
In industries where precision is critical, such as aerospace and automotive, CNC water jet cutting ensures accurate cuts with tight tolerances. Water jet cutters are capable of cutting complex shapes in metals, composites, and glass, making them indispensable in the production of parts and components for these industries.
3. Architecture and Design
Water jet cutters are also used in architecture and interior design for cutting stone, tile, and glass. The precision of water jet cutting allows designers to create intricate patterns and shapes, enabling unique and custom designs that would be difficult or impossible to achieve with other cutting methods.
Machine Tech Enterprises, LLC: Your Partner in Precision Cutting
At Machine Tech Enterprises, LLC, we understand that choosing the right CNC water jet cutter is an important decision for your business. That’s why we offer a range of high-quality water jet cutting machines designed to meet the specific needs of industries from metal fabrication to design and architecture. Our CNC water jet cutters are also built for precision, reliability, and ease of use, helping you achieve the best results for your projects. So if you’re ready to invest in a CNC water jet cutter or need expert advice on selecting the right machine for your business, explore our collection today, and discover how Machine Tech Enterprises, LLC can help you achieve precision cutting with confidence.